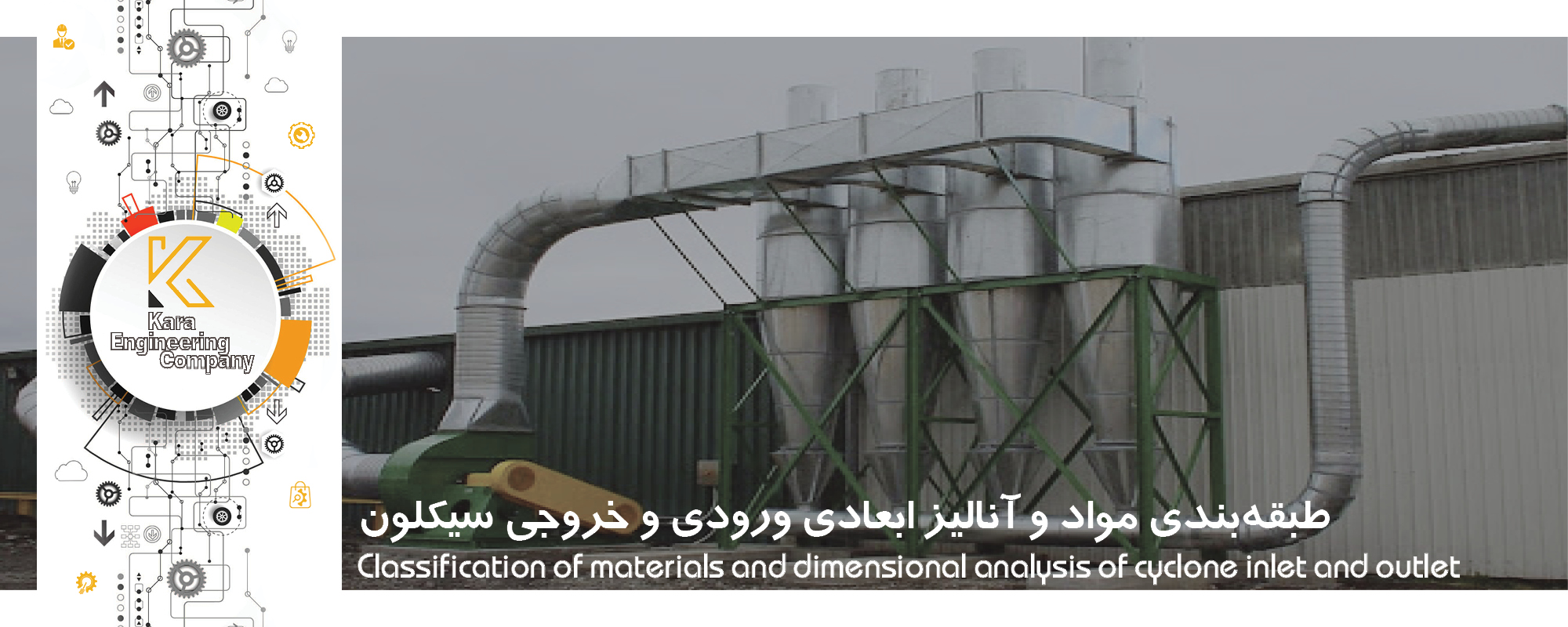
Classification
Classification is a method that divides a mixture of minerals into two or more products based on the speed at which grains fall in a fluid. Because the efficiency of sanders is not suitable for fine particles, the classification of materials in water is used in the ore processing industry.
Because the speed of particles in a fluid depends not only on their size but also on their specific weight and shape, classification principles are also important in gravity calibrators.
Classifiers
Classifiers basically consist of a separator column in which a fluid rises at a constant rate.
Types of classifiers:
Classifiers are divided into two general categories based on the type of flow:
- Classifiers with horizontal flow, such as mechanical classifiers in which the dominant mechanism is free sedimentation and the effect of particle size is obvious.
- Vertical flow classifiers, such as hydraulic classifiers, whose mechanism is sedimentation with a barrier, and density has a great effect on separation.
Spiral Classifiers
Particles with a low sedimentation rate in the liquid are transferred to the overflow.
Particles settle at the bottom of the container with a high settling speed and are pulled up by the spiral in the opposite direction of the water flow.
The movement of the spiral causes the softener to be released and prevents them from entering the upper outlet (coarse particles).
The Hydrocyclone
In hydrocyclone, centrifugal force is used to accelerate the sedimentation rate of particles. Hydrocyclone is the most important device for classifying small particles in the mining industry. The particles move towards the wall with a high settling speed and exit through the opening of the fine sediment.
Due to the action of the fluid resistance, the particles move towards the low pressure area along the axis with a low settling speed and are transported upwards through the diaphragm to the fine head.
Two forces are applied to each particle: the centrifugal force in the outward direction and the fluid resistance force in the inward direction. Particles on the area with zero vertical velocity (Envelope of zero vertical velocity) have an equal probability to transfer to the overflow or exit from the bottom.
The inside of the cyclone can be divided into four regions in terms of particle size distribution.
The unclassified feed enters the narrow area around area A and hits the wall and roof of the cyclone. Region B occupies a very large part of the cyclone cone and contains all classified coarse particles, for better understanding, its granulation distribution is similar to the coarse grain product.
Similarly, all fine-grained particles accumulate in zone C, a narrow zone that starts around the vortex opening and finally extends downwards along the axis of the cyclone. Classification is done only in area D. Within this region, the distribution of granulation is radial, as the dimensions decrease, the radial distance from the axis decreases.
Cyclone Efficiency
The most common method of showing cyclone separation efficiency is by the separation curve. The cut point of a cyclone is usually determined as a point on the separation curve where 50% of the particles are transferred to the bottom.
The greater the slope of the middle part of the separation curve, the higher the efficiency. The slope of the curve is determined by specifying the points where 75% and 25% of the food particles are transferred to the clean. In an ideal cyclone, the defect coefficient is zero.
In the water that is transferred to the bottom, particles are also removed indiscriminately, the amount of which is usually assumed to be proportional to the water transferred from the feed to the bottom.
Effective factors in cyclone efficiency
In order to reach the desired separation, parameters such as feed input, aperture size, fine opening, pulp pressure and dilution ratio should be adjusted.
One of the important parameters of the cyclone is the pressure drop in it (between the inlet and outlet of the overflow). It is recommended that the hydrocyclone be adjusted in such a way that its overflow pressure is close to atmospheric pressure. In this case, the pressure drop is equivalent to the pulp pressure drop in the inlet opening an increase in the feed rate or pressure increases the centrifugal force, and as a result, fine particles are transferred to fine particles. In other words, d50(c) decreases.
By increasing the solid percentage of the pulp, the sedimentation with the barrier and the resistance to the rotational movement increases, and as a result, the coarse particles find their way to the overflow.
For separation in small sizes, the percentage of solids should be low (less than 30%) and the pressure should be high. The most basic parameter of a hydrocyclone is its diameter, and with its increase, the separation limit increases. By increasing the diameter of the overflow opening, the separation limit increases. The diameter of the overflow opening is approximately 0.25-0.45 times the diameter of the inlet opening of the cyclone.
The separation efficiency of hydrocyclones is higher than mechanical classifiers. The separation limit of the air cyclone is 5-50 mm. The capacity of this type of cyclones is high, but their efficiency is low.
Cyclone outlet areas are defined as follows:
- Area: A If the operation is done correctly, it will occur. The formed cone will be at an angle of 20-30°.
- Area: b, the opening of the small bottom causes stringing and the concentration of the pulp is very high. The loss of the air core causes coarse particles to break into overflow
- Area c: The large opening of the bottom causes excessive dilution of the bottom, as a result, unclassified materials are transferred to the bottom along with water.
The effect of the size of the spout opening on the spout product
Several cyclones are used in parallel to increase the capacity. In this series of cyclones, their position angle is not vertical. This work is done for two reasons: increasing efficiency and easier guidance of fine materials to the final output.