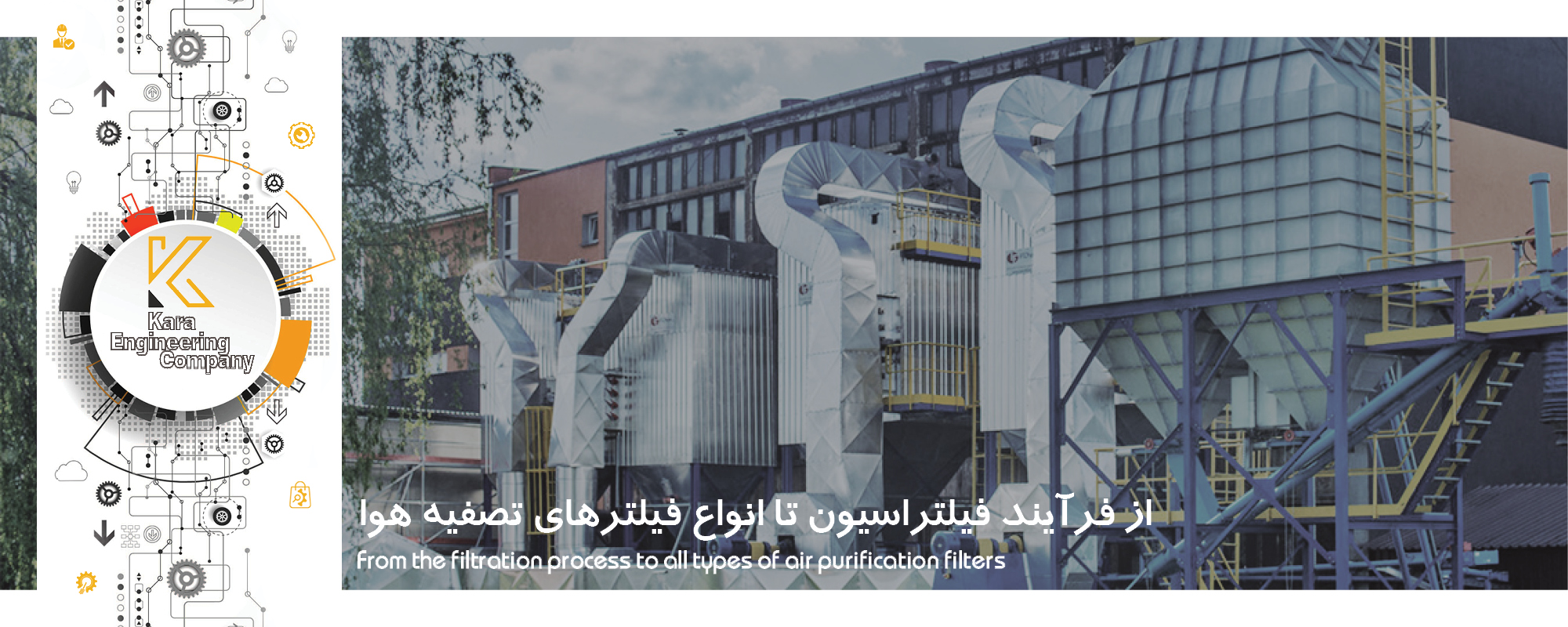
Air filters, which are part of people's living things, are used in kitchen hoods, cars, vacuum cleaners, and masks. Filtration is one of the common mechanisms of air purification and air pollutant sampling. This process is very complex and includes all mechanical principles of particles, gas kinetics and other properties such as electrostatic property. Fibers or other particle trapping materials can be made in different shapes and with different particle collection efficiencies. In some special situations, such as the operating room or electronic industries, it is necessary to use a high-efficiency filter to collect particles.
One of the most popular types of industrial filtration systems is the use of an industrial dust collector or bag filter. This filtration system is widely used in cement factories, iron smelters, metal melting furnaces, foundries, food and pharmaceutical industries, etc.
And it shows high adaptability and maneuverability in any type of industry. It is also very reliable due to its high work efficiency. This system is also known by other names such as bag dust collector or dry dust collector.
The bag filter consists of a chamber in which the bag filters are located. The mechanism of operation of the bag filter is that a centrifugal fan is placed after its outlet, and the centrifugal fan with air suction causes polluted air to enter the bag filter chamber. The air flow path inside the chamber is such that the incoming air must pass through the surface of the bag filters to get out. As the air passes through the bag filters, dust remains on it and clean air comes out of the bag filter compartment.
But in general, the filters used in air purification are in three main groups: granular and fibrous filters (media), HEPA filters, and fabric filters.
Granular and fibrous filters (media)
These filters are called by this name because they can collect the particles according to the aerodynamic diameter inside the components of the filter and in its depth. These filters have different types of fiber and granules. Because the particles are collected in the depth of the filter, it is often difficult to clean them.
Uses:
As a pre-filter to catch large particles before the next collector, which is to increase the efficiency of that device and ultimately increase the efficiency of the system. For example, it is used to collect large dust that is created from furnaces.
Collecting dust that cannot be collected by other types of collecting devices. For example, fibrous filters can be used to collect stuck dust. Fibrous filters are made of woven, felted and knitted materials. The fibers used in the construction of filters are made of linen, polypropylene, fiberglass, nylon, polyester, wood, Teflon, polyamide p84 and ceramics. The selection of filter type is based on media cost, operating temperature, pressure drop and air passage properties such as flammability, corrosion and humidity.
HEPA filters
These filters were initially designed to prevent the movement of radioactive particles in the air, and their efficiency is based on this concentration, so they should only be exposed to air currents that are similar in terms of concentration to the concentration of these particles.
The important thing about these filters is their very high efficiency. The pressure drop in these devices increases slowly and continuously reaches its maximum design value the pressure drop when the filter is new is generally 125-250 pascal. If the filters are not replaced, we will reach the maximum pressure drop in the system, in which case the air passage of the system will decrease and its efficiency will decrease.
These filters are used in a place where very high collection efficiency is considered. These filters have a paper structure that is layered and folded on top of each other to create a very high surface in front of the passage of air to smooth it.
This layered structure reduces the filtration speed and consequently increases the collection efficiency and lower pressure drop. But its design is such that it cannot be cleaned and must be replaced after time passes. The reason for this is that the space between the folds in the papers, which were created to increase the collection efficiency, is very small.
Among the limitations and disadvantages of this purifier can be mentioned the impossibility of cleaning it, low capacity in air purification and use in low dust environments.
HEPA filters are used in places that need very clean air, such as operating rooms in hospitals, clean rooms in electronics and pharmaceutical industries, etc. In these places, the filters make the indoor air cleaner than the outdoor air because they have a high inherent collection efficiency, they can be used as the second collector in the ventilation system. It is recommended to place two filters in series and back to back in the systems where this filter is used. In this case, if the first filter fails, the second collector protects the employees. Now, if there is only one filter and this filter fails without the employees noticing, they are exposed to contamination.
Fabric filters
Fabric filters are widely used in industrial environments and in local ventilation systems. This device consists of a chamber in which the filters are located. The working mechanism of this device is that a fan is placed after its outlet, and the fan with air suction causes polluted air to enter the chamber.
The air flow path inside the chamber is such that the incoming air must pass through the surface of the filters to exit. As the air passes through the filters, dust remains on it and clean air comes out of the chamber outlet.
Compared to the previous two groups, these filters can mostly be cleaned. In general, these filters are cleaned based on four methods: shaking, reverse flow, jet pulse air and sonic.
Shaking is the oldest and easiest way to clean fabric filters. Its mechanism of action is that the upper part of the filters is connected to a number of oscillating devices directly and horizontally or vertically. When the oscillating device starts to oscillate, the dust on the filter is removed from it and falls into the hopper part of the device and exits the system.
Oscillation and shaking is done by a motor that can be operated either automatically or manually by the operator. In industries and small units, this operation is done by the operator with a lever that is connected to the filters, and often the motor is not used for oscillation.
In some filter houses that have a vibration mechanism to dedust the filter, a gentle reverse air flow passes through the cloths, which helps to collect the dust from it. Cleaning filters by reverse air flow requires a system of dampers to cut off the main air flow and open the reverse air flow.
The ends of the bag filters are connected to a metal plate and the other side of them is suspended above the dust collector. This type of industrial dust collector consists of several parts to enable continuous operation for the filtration system.
This leads to the complexity of the design and operation of the filter house and increases the installation and implementation costs. As a result, reverse air flow is used only in relatively large filter houses, where the vibration system alone is not able to remove dust from the filters.
Filtration in systems with high outlet air temperature requires the use of special fabrics. For example, fiberglass filters can be used in such environments. Of course, we should not forget that each fabric or filter has its own thermal resistance. For example, fiberglass filters cannot be used at very high temperatures in such cases, you can use fabrics made of ceramic cement. It should also be noted that various factors are involved in choosing the filter and the type of cleaning system. For example, fiberglass filters are not resistant to vibration and vibration causes them to be destroyed. Therefore, reverse air flow without vibration should be used for this filter house. Such systems usually require bags with a special surface to increase the release of dust.
In the last method, the filter is cleaned using a high-pressure air flow, which is known as the jet pulse method. In this method, each bag filter is supported separately by a metal cage, which air enters with high pressure from the upper part of the filter and causes dust removal of the filters and as a result they are collected.