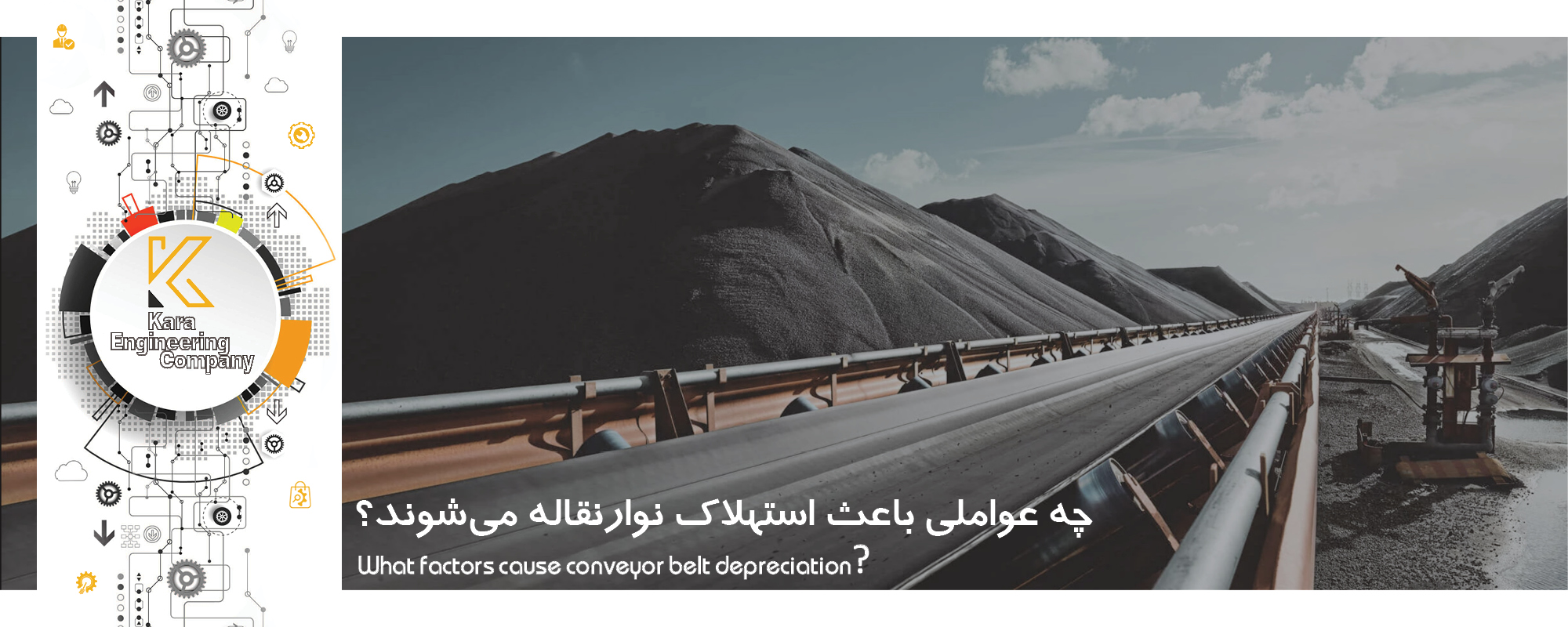
One of the common problems in conveyors is the severe wear of their output shot. Also, another major problem in belts (arched conveyors) is the lifting of the belt from the rollers in the arc, which results in the deviation of the belt from the rollers and causes material to spill out. In some industries, it may be thought that designing a conveyor means: choosing a belt size and possibly a motor and gearbox and nothing else. In this way, only a few pages can be enough to design a conveyor belt, and anyone can become a conveyor belt designer in one day. In the event that various books and handbooks have been written for the design of this equipment, and various manufacturers have provided various tables. A superficial look at this important issue creates problems that some factories have been struggling with for years.
Falling of materials and their collision with the exit shot
One of these problems is how materials fall and collide with the output shot. Failure to pay attention to this issue causes a lot of noise and rapid wear of the sheets, and finally, in a short period of time, parts of the steel sheet are destroyed, and the removal of materials from it causes many problems for the factory. The common solutions used in different factories to control this problem are:
- Use of anti-wear sheets: Many mechanics managers use anti-wear sheets to solve this problem. With this method, the wear time increases, but the impact sound of the materials does not decrease. However, the problem reappears after a while and this cycle repeats itself.
- Using boxes filled with cement mortar: In some cement factories and mines, by creating a box outside the shot sheet and filling it with cement mortar, they transfer this wear to the concrete. Here, the sound is reduced, but the concrete cannot withstand the continuous impact and crumbles. Therefore, in addition to the continuous lubrication of the bearings, continuous concreting is also added to the maintenance. It should be noted that although this cementing method can be used in cement factories and similar, it is not allowed in the health and food industries.
Design solutions: The solution to this problem is the correct redesign of the tape output shot. This method solves the problem once and for all. Conveyor retrofitting may be costly at first, but in the long run it will reduce costs and avoid additional workers and repairs. There are two solutions in the design of this part:
- Design of tank shots (stepped): by calculating the throwing movement and the place of separation of the material from the money, which depends on the speed of the tape, gravity and the height of the material on it; The place of collision can be determined with good accuracy. Therefore, we make the part of the shot wall where the material collides in a stepped manner. In this way, first some of the material sits on the stepped surface and the rest of the material flows down. In this case, the materials lose their speed and impact after hitting the previous materials and fall in the middle of the shot. With this, we have used an anti-wear plate for life and the life of the shot has been multiplied.
- Design based on not hitting the shot wall: in this method, it is tried that the material does not collide with the body. This method is used in equipment that has a short distance from the next device or that is not affected by the fall of materials; such as material falling into storage tanks. If the distance between the snoring shot and the receiving device is long, an adjustable plate is used. This arc plate, which is made of replaceable anti-wear sheets, is placed at a distance less than the movement of material throws. which causes material to move - not material impact - on it. Among the advantages of this method can be mentioned the adjustability of the moving screen and the reduction of the noise produced. The problem of replacing wear plates and the need to open and close a number of parts is one of the disadvantages of this method.
The issue of the tape lifting from the rollers at the arch location
One of the most important things in conveyors is the arc radius of the belt at the place where the movement changes from horizontal to inclined and vice versa, which is called concavity and convexity. . The basis of the design in calculating the concavity is the radius in which the tape does not lift off the rollers due to the tension force, and the peak of this problem occurs when the tape is empty. For example, in one of the factories, the tape that takes the materials to an underground tunnel due to the failure to calculate this radius after adjusting the balance weight of the tape rises about one meter from the rollers and hits the roof of the tunnel, which is more of a problem at the start time will happen especially when the bar is empty. Different factors can cause this problem:
- Abrasion of the tape over time: Conveyor belts have two protective layers, one under the tape and the other on the tape, which are worn over time and their weight decreases, or after replacing the tape due to the lack of a model in the market and replacing it with Another type is faced with weight difference problems. Therefore, if the tape becomes lighter, it will rise from the rollers in the arc-shaped part. Of course, the amount of this issue is small and can be ignored.
- Excessive amount of tension weight: In some factories, due to the fact that the required weight of the tension weight of the tape is not written in the map or the maps are not available, this is done experimentally. Sometimes this number is more than the required amount which causes the belt to bounce and its rotation on the tape drive pulley, and the cover on the pulley and the tape are both damaged.
- Failure to correctly calculate the radius of the arc: strips that pass through tunnels or have structures around them face many problems; Because the structures are built in advance and face the limitation of the upper space.
To avoid such problems, the tension of the tape should be calculated first. Then get the tension in the desired area. After that, with the available weight of each meter of the conveyor belt, it is possible to calculate the radius of the vertical arc of the belt (concavity) and draw the boundaries of the construction plans. As you know, there are many tips about each part of the conveyor belt. Also, environmental conditions such as wind, sun, etc., as well as the type of material (coarseness, moisture, dryness, adhesion, etc.) cause changes in the design of the conveyor belt. For example, the design of a conveyor belt in the north of Iran for transporting clay is different from a conveyor belt in Kerman province with exactly the same specifications, or for a conveyor belt for transporting wheat or flour, it will definitely be different.
Therefore, copying blindly and not paying attention to all issues can bring many and irreparable problems and costs for factories. Because they cannot tear down and throw away the incomplete facilities and build new facilities again, and neither the built device is their answer. So they have to burn and build with an incomplete machine. Hoping that with the one-time cost of making the conveyor belt, we can use it for years without any problems.